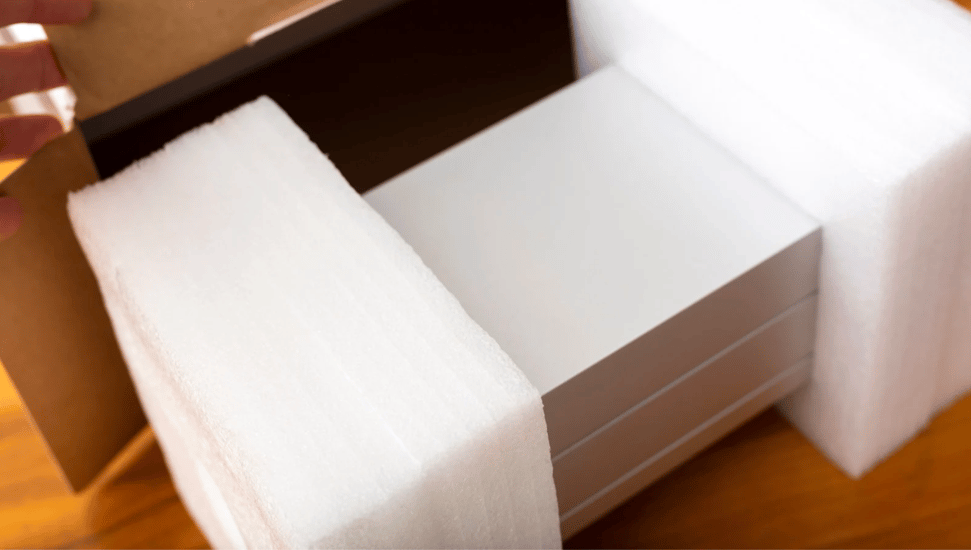
Custom Foam Inserts: Elevating Product Presentation and Protection
Custom foam inserts play an important dual role in showcasing consumer and commercial products while keeping them safe and secure.
Polyurethane foam can be engineered by Sterling Manufacturing’s Design and Testing department into packaging solutions that elevate your product presentation and protection.
“Polyurethane packaging foam (PPF) can provide more cost-effective, form-fitting cushioning that uniquely and securely [protects] items that need to stay safely in place during transit,” says the Center for the Polyurethanes Industry (CPI). “PPF is widely used to safely protect and transport many items, such as electronic and medical diagnostic equipment, delicate glassware and large industrial parts.”
Think of custom foam inserts as a majestic-looking thoroughbred, who behind the scenes is a real workhorse as its protective layer provides cushioning and absorbs shocks while its aesthetics boost your brand perception.
Let’s look at the importance of custom foam inserts in both protecting products and enhancing their presentation.
Benefits of Custom Foam Inserts
The benefits of custom foam inserts are not limited to product presentation and protection but extends to organization, compliance and sustainability.
Custom foam inserts can even be a cost-effective solution vs. “pick and pluck” foam options as you will save in the long run with reduced shipping costs and product replacement for damaged items, and custom foam inserts cut down on the manual labor required to package items.
Here’s a closer look at the benefits of custom foam inserts:
- Protection and Safety: Custom fit reduces movement and damage during transit as custom foam inserts are effective against impact, vibration and rough handling. This protection and safety are crucial for fragile, high-value or irregularly shaped items.
- Enhanced Presentation: Custom foam inserts can elevate brand image and perceived product value with professional and premium unboxing experiences. This is important for luxury goods, technology, and custom manufacturing.
- Organization and Compliance: Industry-specific standards for storage and transport can be met by custom foam inserts. They also keep items organized while reducing the risk of loss or damage. Workplace safety is also enhanced as tripping hazards are minimized when tools and other items are always in their proper place.
- Sustainability: Many custom foam options are recyclable or reusable, which reduces waste and supports eco-friendly initiatives.
- Cost-Effectiveness: Foam inserts are lightweight, which can reduce shipping costs, while also durable enough to withstand handling and transport. By protecting products effectively, custom foam inserts can lead to long-term savings by reducing the need for repairs or replacements.
These benefits highlight why custom foam inserts are a valuable solution for businesses seeking to enhance product protection, presentation and customer satisfaction while maintaining sustainability and cost efficiency.
Applications Across Industries
Custom foam inserts find applications across various industries, providing tailored protection and presentation solutions for a wide range of products.
“Polyurethanes, some of the most versatile plastic materials in use today, are critical to a variety of applications and products that help enhance our everyday lives,” says the American Chemistry Council.
Custom foam inserts can be found across many industries, including:
- Electronics and Technology
o Protects sensitive components like laptops, cameras and analytical instruments
o Safeguards electronic devices, computers and technologically sensitive equipment during transit
o Ideal for packaging monitors, televisions and audio/visual equipment - Medical and Pharmaceutical
o Secures medical devices, surgical instruments and pharmaceutical products
o Ensures safe transport of sensitive medical equipment and supplies
o Protects prosthetics and other specialized medical products - Military and Aerospace
o Safeguards military equipment and firearms
o Provides protection for sensitive aerospace components - Luxury Goods and Artwork
o Enhances presentation and protects valuable items like jewelry and watches
o Secures framed artwork and delicate collectibles
o Ideal for wine and liquor bottle packaging - Industrial and Scientific
o Protects industrial equipment, tools and precision instruments
o Safeguards scientific instruments and analytical devices - Music and Entertainment
o Secures musical instruments, especially guitars and fragile equipment
o Protects microphones and sound equipment - Automotive and Manufacturing
o Safeguards automotive parts and accessories
o Protects custom manufacturing components and precision tools
“Flexible foam can be created in almost any variety of shapes and firmness. It is light, durable and supportive,” says CPI.
These applications demonstrate the versatility of custom foam inserts in providing tailored protection and presentation solutions across diverse industries, from high-tech electronics to delicate luxury goods.
Design and Fabrication Techniques: Custom Foam Inserts
Custom foam inserts can be designed and fabricated using various methods, each with its own advantages. Here are some key design and fabrication techniques used in the industry:
- Design Methods
o CAD Software: Designers can test and refine designs before fabrication with this computer-aided design software. Adjustments, iterations and precise measurements are made simple with CAD tools. This technology is continually improving with 3D visualization now standard.
o Paper Method: A simple and cost-effective design method for smaller projects is creating paper templates to map out designs. This can be suitable for modifying existing cases or containers. - Fabrication Techniques
o Die-Cutting: Uses steel rule dies to stamp out shapes from foam sheets. This is a fast and efficient fabrication technique for high-volume production. It is also cost-effective for large quantities.
o Contour Cutting: Follows the outline of the profile of a specific shape. This method is ideal for creating custom-fit foam inserts for irregularly shaped items. This fabrication technique can be done manually or with specialized machinery utilizing CAD-CAM drawings for increased precision.
o Convoluting: Creates a wave-like or egg-shaped pattern on the foam surface which can enhance cushioning properties and flexibility for packaging. Often used in mattresses and seating applications for improved comfort.
o Dimensional Cutting: Involves cutting foam to specific dimensions or thickness. This method, also called vertical or horizontal cutting, can be useful for creating layered inserts or precise foam blocks. Dimensional cutting is often used in combination with other techniques for final shaping.
o Laminating and Bonding: Combines multiple materials or foam layers. Techniques include flame lamination, heat bonding and adhesive application. This method is used to create composite materials for specific requirements.
When choosing materials for custom foam inserts, it's crucial to consider the specific requirements of your product and shipping conditions. Here are some of the most used materials:
- Polyethylene (PE) Foam: Durable and strong cushioning properties plus PE is water-resistant and non-abrasive. Excellent for heavy-duty applications as well as flexible and resilient, maintaining shape after compression.
- Polyurethane (PU) Foam: Superior shock absorption and vibration dampening. PU conforms closely to product shapes making it excellent for protecting fragile items like electronics. Open-cell structures make for better air circulation.
- Expanded Polystyrene (EPS) Foam: Lightweight yet strong with excellent thermal insulation properties, EPS is cost-effective for high-volume production and ideal for packaging consumer electronics and appliances.
Sterling Manufacturing can offer custom features for your foam inserts such as color options, multi-layering, compartmentalization, surface finishes, anti-static and anti-abrasive foams.
Contact Sterling today to learn more about how we can design and fabricate custom foam inserts that will keep your products protected while enhancing your end-user experience.
Leave a Comment
Your email address will not be published.